магазин
grinding function of cement plant
KEFID,Дробильно-сортировочное оборудование Китая высокого качества, стандартное дробильное оборудование. На протяжении более 30 лет мы занимаемся исследованиями и разработками и производством дробильного оборудования, дробления зданий, промышленных дробилок и экологически чистых строительных материалов, и предлагаем профессиональные решения и дополнительные продукты для создания ценность для клиентов.
Онлайн сообщение
grinding function of cement plant
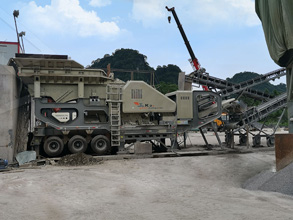
Cement Grinding unit Technomart India (Ahmedabad)
Apr 14, 2015· Cement Grinding unit Technomart India (Ahmedabad) Dryers and Graders, Process And Storage tanks, Cement Block Machines, Cement Grinding Plant, Cement Kiln, Cement Machinery, Cement MixersJan 21, 2015· Coal grinding plant LM190M vertical mill in Jordan COAL CRUSHER PLANT 500 TPH di buat oleh PT NUSA DUA MAKMUR (SUKIDI1) Duration: 7:13 Sukidi Erlangga 79,197 viewsCoal grinding plant LM190M vertical mill in Jordan
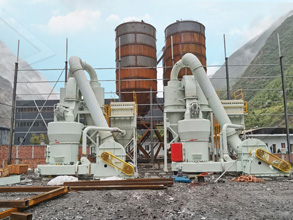
Cement mill Wikipedia
A cement mill (or finish mill in North American usage) is the equipment used to grind the hard, nodular clinker from the cement kiln into the fine grey powder that is cementMost cement is currently ground in ball mills and also vertical roller mills which are more effective than ball mills3) OnSite Power Plants Cement manufacturing is a very energy intensive process As such, onsite power plants are increasingly being used to meet energy demands of the cement plant Some of the fire hazards associated with onsite power plants include fire in power house buildings due to ignition of lube oilFire and Explosion Hazards in Cement Manufacturing Industries
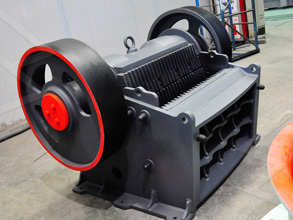
Grinding Mills: Ball Mill & Rod Mill Design & Parts
In a typical cement plant employing closed circuit grinding, 1750 surface can be obtained with a finish grind of between 93 and 96% passing 200 mesh This area requirement means that fines are not only desirable but necessary, and that a size analysis must show a distribution of material from approximately 80 microns down to less than one micronhandling & Grinding, coal grinding, preheater kiln & cooler, Clinker grinding (cement mill), packing plant & Loading plant, quality control It also provides the brief description about the machinery used in each stage and its working principles Cement industry has come a long way in technological up gradation,Volume 3, Issue 5, November 2013 Study of Processing and
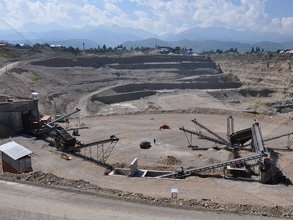
IMPROVING THERMAL AND ELECTRIC ENERGY
Improving Thermal and Electric Energy Efficiency at Cement Plants: International Best Practice 1 Cement production is a resourceintensive practice involving large amounts of raw materials, energy, labor, and capital2010 survey, Essroc Cement Co’s Essexville grinding plant ceased operations and Essroc’s grindingonly facility in Nazareth, PA was combined with their clinkerproducing plant – bringing the number of grindingonly plants to seven US cement manufacturing is primarily a fossil fuel fired industry with 917% of all plants using coalUS Portland Cement Industry: Plant Information Summary
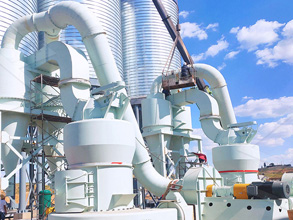
function of cement clinker processing plant
Burning cement clinker in rotary kiln is the key step of the production, it will directly affect the quality of the cement clinker 6Cement Grinding Cement grinding is the final process of cement manufacture, but also the most power hungry process Its main function is to cement clinker (and gelling agent, performance adjustment material etcZimbabwe: Chinabased SinoZimbabwe Cement Company and LiveTouch Invest, owner of Diamond Cement Zimbabwe, have acquired a six hectare site in the coal mining area of Hwange, Matabeleland North Province, and announced a planned investment of US$30m in the construction of a grinding plant which will grind clinker with waste materials from coal extraction to produce cementgrinding plant Cement industry news from Global Cement
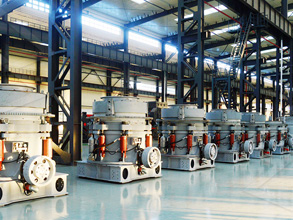
Raw Material DryingGrinding Cement Plant Optimization
Ball Mill Ball mills with high efficiency separators have been used for raw material and cement grinding in cement plants all these years Ball mill is a cylinder rotating at about 7080% of critical speed on two trunnions in white metal bearings or25 years in the cement industry supplying engineering and equipment for assembly and commissioning of clinker and slag Grinding Station, cement plants, cement silos, vertical mills, horizontal mills, PLUG&GRIND modular and portable grinding stations 25 años en la industria del cemento suministrando ingenieria y equipos para montaje y puesta en marcha deCEMENGAL Engineering, equipment and assembly for the
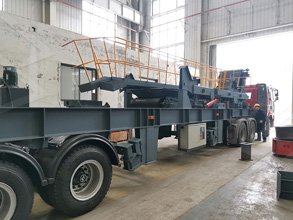
LOESCHEMILLS
1990 Central coal grinding plant (LM 263 D) for gas and steam power station (coal gasification) 1992 Central coal grinding plant (LM 263 D) for the production of lignite (brown) coal dust 2002 Coal grinding plant (LM 232 D) for grinding wood pellets for power stations 2005 First 4roller pressure mill (LM 434 D) becomes availableJul 31, 2014· Grinding process modelling and simulation methods can be used for optimisation A case study conducted using the data from an industrial cement plant indicates that: • Precrushing of cement clinker using a Barmac crusher offers realistic benefits to a cement plant in terms of process efficiencyCement Grinding Optimization LinkedIn SlideShare
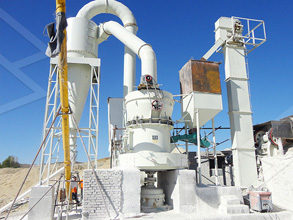
116 Portland Cement Manufacturing
Portland cement manufacturing plants are part of hydraulic cement manufacturing, which also includes natural, masonry, and pozzolanic cement accomplished during grinding in ballandtube mills or roller mills While thermal energy for drying as a function of locationCement grinding is the final process of cement manufacture, but also the most power hungry process Its main function is to cement clinker (and gelling agent, performance adjustment material etc) grinding to appropriate particle size (such as fineness, specific surface area) o form a certain grain size distribution, increase its hydration areaCement Manufacturing Process Flow Chart
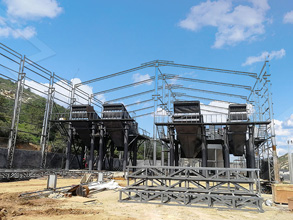
LOESCHEMILLS
1990 Central coal grinding plant (LM 263 D) for gas and steam power station (coal gasification) 1992 Central coal grinding plant (LM 263 D) for the production of lignite (brown) coal dust 2002 Coal grinding plant (LM 232 D) for grinding wood pellets for power stations 2005 First 4roller pressure mill (LM 434 D) becomes availableJul 31, 2014· Grinding process modelling and simulation methods can be used for optimisation A case study conducted using the data from an industrial cement plant indicates that: • Precrushing of cement clinker using a Barmac crusher offers realistic benefits to a cement plant in terms of process efficiencyCement Grinding Optimization LinkedIn SlideShare
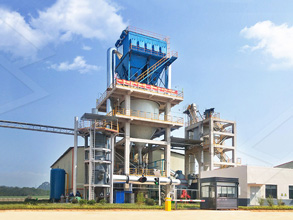
116 Portland Cement Manufacturing
Portland cement manufacturing plants are part of hydraulic cement manufacturing, which also includes natural, masonry, and pozzolanic cement accomplished during grinding in ballandtube mills or roller mills While thermal energy for drying as a function of locationCement grinding is the final process of cement manufacture, but also the most power hungry process Its main function is to cement clinker (and gelling agent, performance adjustment material etc) grinding to appropriate particle size (such as fineness, specific surface area) o form a certain grain size distribution, increase its hydration areaCement Manufacturing Process Flow Chart
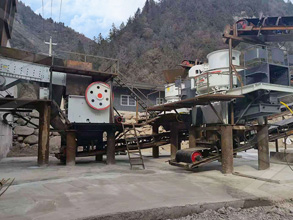
cement plant equipments manufacturer and suppliers of
Ashoka's cement plant unit has continued focused on objectives of product improvement and quality In our entire turnkey cement plant equipments and machinery, we supply a complete assembly consisting of different machines and equipment, which facilitate the plant to execute efficiently and manufacture a betterquality completed product as per the international quality standardsVizag Grinding Unit, Gobburupalem Village, Visakhapatnam Andhra Pradesh (095 MTPA) This Grinding unit with a capacity of 095 MTPA is located near Visakhapatnam was commissioned in March 2015 This plant is located just on NH 5 located in between Yellamanchilli and AnakapallyGrinding unit Vizag | Ramco grinding unit in Vizag
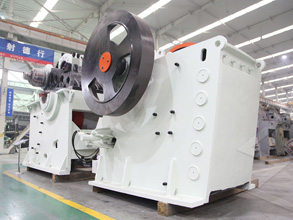
Technical Support Document for Process Emissions from
Jan 28, 2009· cement plants, excluding Puerto Rico (PCA 2006) It includes 107 integrated cement plants that house both kilns for producing clinker and mills for grinding cement from clinker, and 8 fine grindingonly plants that do not produce clinker and house only grinding mills for producing cement from purchased clinkerImproved Cement Quality and Grinding Efficiency by Means of Closed Mill Circuit Modeling (December 2007) Gleb Gennadievich Mejeoumov, BS, Ivanovo State Power University, Russia; MS, Ivanovo State Power University, Russia Chair of Advisory Committee: Dr Dan Zollinger Grinding of clinker is the last and most energyconsuming stage of the cementIMPROVED CEMENT QUALITY AND GRINDING EFFICIENCY
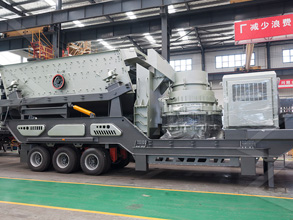
PROCESS CONTROL FOR CEMENT GRINDING IN VERTICAL
The VRM is a type of grinding mill integrated with multi functions such as grinding, drying and separation, used for grinding of coal, petroleum coke and minerals Most recently this technology has been employed for comminution of Blended, Slag and Port Land cement grinding The cement grinding and dryingThe only common feature in all cement production plants is the difficulty of grinding the source material as the material is hard enough and has high abrasiveness That is why high quality grinding balls with high hardness over the entire section are used during grinding materials in tube mills in this industryRAW MATERIALS IN CEMENT PRODUCTION Primo Pizza
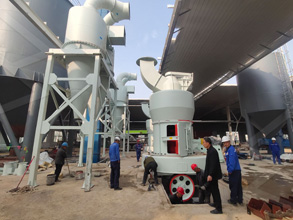
The Effect on the Performance of Cement Grinding Aid
(17 mm), gypsum and grinding agent to join together Φ 500 x 500 national cement plant in the unified test standard laboratory mill grinding together, each time grinding 5 kg, grinding time for 40 min, the release time for 5 minJK Cement will be implementing the vertical roller technology at this plant which will cut down the power consumption, reduce the grinding cost and will enhance the production performance The Company is looking forward to making this unit operational by Q4 of the next financial yearJK Cement setting up grinding unit in Balasinor & Aligarh
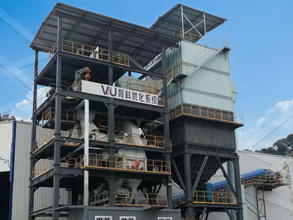
Simulation of clinker grinding circuits of cement plant
Particle size distributions of obtained samples from several sampling campaigns were determined and raw data were mass balanced before being used in simulation studies After determination of breakage function, selection function, Bond work index, residence time distribution parameters, and Whiten’s model parameters for air separators and diaphragms between the two compartments of tube ballThe results show that approximately 248t, 469t, and 341t of materials are required to produce a ton of the product in raw material preparation, clinker production, and cement grinding stages(PDF) Analysis of material flow and consumption in cement