магазин
synthetic sand in conrete manufacturing
KEFID,Дробильно-сортировочное оборудование Китая высокого качества, стандартное дробильное оборудование. На протяжении более 30 лет мы занимаемся исследованиями и разработками и производством дробильного оборудования, дробления зданий, промышленных дробилок и экологически чистых строительных материалов, и предлагаем профессиональные решения и дополнительные продукты для создания ценность для клиентов.
Онлайн сообщение
synthetic sand in conrete manufacturing
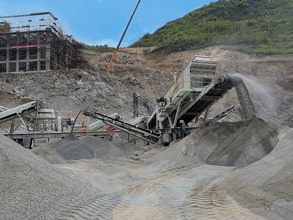
Use of Manufactured Sand in Concrete and
Manufacturing of Sand process involves three stages, crushing of stones in to aggregates by VSI, then fed to Rotopactor to crush aggregates into sand to required grain sizes (as fines) Screening is done to eliminate dust particles and Washing of sandimportant Very fine sand is not recommended for concrete purpose The fines content in the sand below 600 microns should be about 30 to 50 % This will be a ideal sand for concrete work as well as masonry and plaster work At present it is generally observed that the fine content in river sand below 600 microns are very less:: ARTIFICIAL SAND
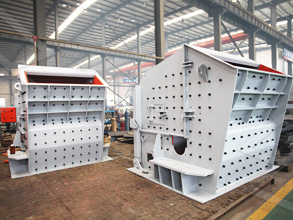
(PDF) A REVIEW ON NEED OF MANUFACTURED SAND IN
With manufactured sand marketed as a material complying with certain recognized specifications, it is then up to the design engineers or concrete producers to specify ordinary crushed rockThe synthetic aggregate for use in concrete is a composite material of recycled plastic having a filler encapsulated in the plastic The synthetic aggregate includes between 30% and 50% recycledUSB1 Synthetic aggregate for use in concrete
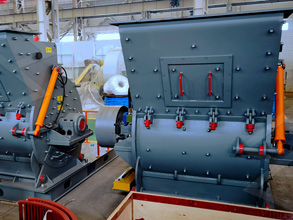
SYNTHETIC AGGREGATES TECHNOLOGIES Products and
Use of synthetic aggregates in the housing industry would contribute to significant reduction of solid waste currently sent to landfills, such as plastics, fly and bottom ash, and polystyreneOther industries that would also benefit most from new synthetic technology are companies and manufacturers needing Lightweight Aggregate meeting ASTM C330, or C331 specifications, or Lightweight Concrete (Ready Mix) Synthetic aggregates can be used as part of the concrete mix in Insulated ConcreteNatural sand has an ideal shape for use as fine aggregate in concrete The natural sand particles are wellrounded and are usually nearly spherical Spherical particles decrease the percentage of voids within the concrete mixture so no additional paste is required to fill these voids Wellshaped natural sands are ideal for workability of mixturesManufactured Sand vs Natural Sand Concrete, Sand,
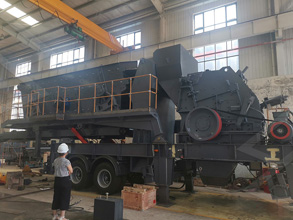
(PDF) USE OF SILICA SAND AS CEMENT REPLACEMENT IN
Results showed that silica sand (upto12%) can effectively being used as partial replacement of cement in concrete without compromising the strength of concrete 2 Compressive strength of silica30102013· By establishing the correct synthetic sand, binder and coating combination it is possible to utilise a single sand type, eliminating the use of expensive speciality sands for mould facing This will allow for an optimised sand reclamation process that minimises new sand purchases and dumping costs, whilst additionally eliminating the formation of silica dust that may contribute to a respirableCharacteristics of synthetic sand and application of
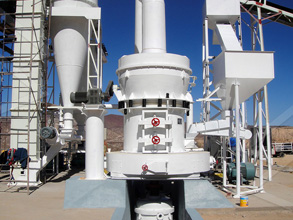
6 Facts about Synthetic Gypsum FEECO International Inc
Synthetic gypsum is used interchangeably with natural gypsum in a number of applications Examples of products that utilize synthetic gypsum include: Cement; Drywall; Glass Manufacturing; Plaster; Soil Amendments; 5 Benefits to Using Synthetic Gypsum Manufacturing synthetic gypsum creates many positive economic and environmental benefitsManufacturing of Sand process involves three stages, crushing of stones in to aggregates by VSI, then fed to Rotopactor to crush aggregates into sand to required grain sizes (as fines) Screening is done to eliminate dust particles and Washing of sandUse of Manufactured Sand in Concrete and Construction
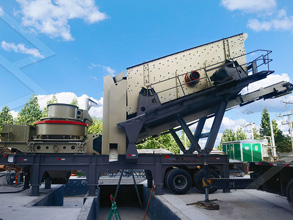
SYNTHETIC AGGREGATES TECHNOLOGIES Products
Synthetic aggregates can be used as part of the concrete mix in Insulated Concrete Forms (ICFs), and in Prestress/Tiltup Concrete, Concrete Roof Shingles, Concrete Wall Board, Stucco, Concrete Block, Concrete Pavers, Concrete Wall Stone (Cultured Stone), Concrete Dry Mix (Bags), Well Cementing and Grouting, Culvert Pipe, Concrete Underground Vessels, Foundations, Pan Floors/Decking, GeoSize, shape, texture play an important role in workability of concrete With more surface area of sand, the demand for cement and water increases to bond the sand with coarse aggregates The control over these physical properties of manufacturing sand make the concrete require less amount of water and provide higher workable concreteManufactured Sand (MSand) for Concrete Properties
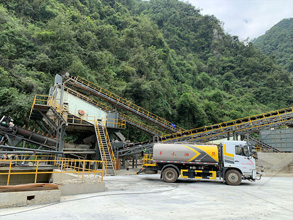
Concrete, a CenturiesOld Material, Gets a New Recipe
11082020· Sand in storage at a plant owned by Central Concrete, which is experimenting with new processes for concrete manufacturing to cut carbon emissionsAdditionall y, using synthetic aggregates in concrete can decrease landfill 131 cost of raw materials used for manufacturing RPA such as LLDPE, dune sand and fly ash are 534 (PDF) Production of Recycled Plastic Aggregates and Its
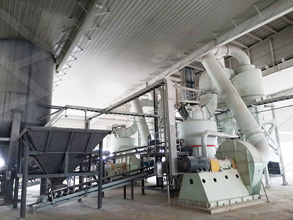
A Research Paper on the Performance of Synthetic Fibre
manufacturing, then it is known as Fibre Reinforced Concrete Different types of fibres may be used in concrete such as steel fibres, glass fibres, synthetic fibre and even natural fibre Synthetic fibre reinforced concrete uses plastic and nylon fibres for enhancement of the strength of concrete SyntheticBuy high quality Synthetic Rutile Sand by Alliance International Supplier from India Key Usage of Silica Sand Silica sand is utilized for water purification and manufacturing of glass, synthetic foundry moulding and higher concrete strengths Silica Fume is typically grey in colour and is categorised as a supplementarySynthetic Rutile Sand by Alliance International Supplier
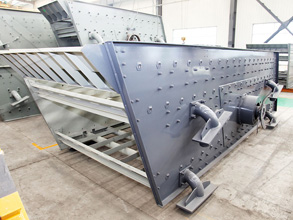
M Sand Vs River Sand (Natural Sand)
Higher concrete strength compared to river sand used for concreting Lesser concrete compared to M Sand Silt Content Zero silt Minimum permissible silt content is 3% Anything more than 3% is harmful to the concrete durability We can expect 5 20% slit content in medium quality river sand Over Sized Materials 0% Since it is artificiallySand for Foam Concrete The maximum size of sand used can be 5mm Use of finer sands up to 2mm with amount passing through 600 micron sieve range from 60 to 95% Pozzolanas The supplementary cementitious materials like fly ash and ground granulated blast furnace slag have been used widely in the manufacture of foam concreteFoam Concrete Materials, Properties, Advantages and
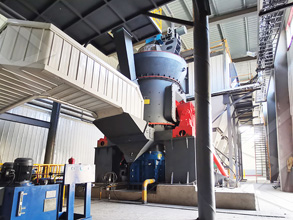
How Cement Is Made
Concrete is formed when portland cement creates a paste with water that binds with sand and rock to harden Cement is manufactured through a closely controlled chemical combination of calcium, silicon, aluminum, iron and other ingredientsSize, shape, texture play an important role in workability of concrete With more surface area of sand, the demand for cement and water increases to bond the sand with coarse aggregates The control over these physical properties of manufacturing sand make the concrete require less amount of water and provide higher workable concreteManufactured Sand (MSand) for Concrete Properties
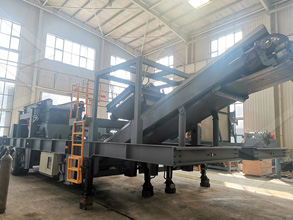
Blue Planet | Economically Sustainable Carbon Capture
Using Blue Planet products the carbon footprint of a cubic yard of concrete can be not just reduced, but the cubic yard of concrete can become carbonnegative by two specific methods: First, by replacing conventional fine and coarse aggregate (sand & gravel) with Blue Planet synthetic limestone aggregate, which is 44% by mass CO2 now converted to a permanent crystalline solid state in CaCO3, the entiremanufacturing, then it is known as Fibre Reinforced Concrete Different types of fibres may be used in concrete such as steel fibres, glass fibres, synthetic fibre and even natural fibre Synthetic fibre reinforced concrete uses plastic and nylon fibres for enhancement of the strength of concrete SyntheticA Research Paper on the Performance of Synthetic Fibre
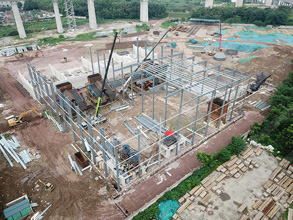
Utilization of waste foundry sand (WFS) in concrete
01092011· The mixture proportion on concrete made with chemical foundry sand was 300 cement, 4475 kg foundry sand, 3996 kg natural sand, and 1150 kg coarse aggregates per cubic meter of concrete, with water–cement of 061, where was proportion of concrete mixture with green foundry sand was 300 cement, 326 kg foundry sand, 458 kg natural sand, and 1150 kg coarse aggregates with24092020· These are the synthetic materials that changed manufacturing for good Concrete Ancient Roman builders combined volcanic ash with burned limestone and seawater and used more than 5,000 tons of it to create structures such as the Pantheon, which are still standingEveryday Synthetic Materials That Changed Manufacturing
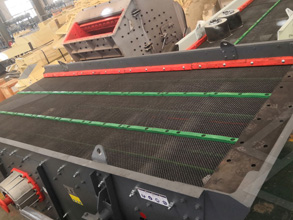
Foam Concrete Materials, Properties, Advantages and
Sand for Foam Concrete The maximum size of sand used can be 5mm Use of finer sands up to 2mm with amount passing through 600 micron sieve range from 60 to 95% Pozzolanas The supplementary cementitious materials like fly ash and ground granulated blast furnace slag have been used widely in the manufacture of foam concreteQuartz Silica Sand is mostly used in foundry, construction, abrasive blasting, railroad, water purifier and other purposes These sands are highly appreciated by our valuable clients Quartz Sand is extensively used in various industrial requirements as construction, water purifier, concreting, waterproofing, as a bed material for boilersSynthetic Rutile Sand by Alliance International Supplier
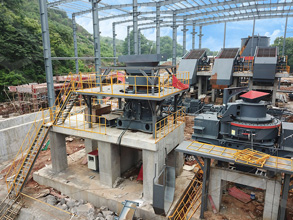
SAND, SAND ADDITIVES and SAND PROPERTİES
Synthetic Sands ` A synthetic sand consists of natural sand with or without clay, binder and moisture ` The organic matter is not present in synthetic sand ` Synthetic sand is a formulated sand, formulation is done to impart certain desired properties not possessed by natural sandAdding a highpurity natural pumice pozzolan to the concrete formulation mitigates or completely eliminates the problems inherent in standard concrete ASTMstandards research has shown natural pumice pozzolan provides significant performance increases in terms of appearance, impermeability, longevity, thermal cracking, resistivity to chemical attacks, and compressive strengthPumice and Concrete: Applications and Benefits of Pumice
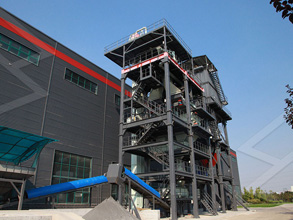
MIT students fortify concrete by adding recycled plastic
Concrete is, after water, the second most widely used material on the planet The manufacturing of concrete generates about 45 percent of the world’s humaninduced carbon dioxide emissions Replacing even a small portion of concrete with irradiated plastic could thus help reduce the cement industry’s global carbon footprint