магазин
blasting coal technology process
KEFID,Дробильно-сортировочное оборудование Китая высокого качества, стандартное дробильное оборудование. На протяжении более 30 лет мы занимаемся исследованиями и разработками и производством дробильного оборудования, дробления зданий, промышленных дробилок и экологически чистых строительных материалов, и предлагаем профессиональные решения и дополнительные продукты для создания ценность для клиентов.
Онлайн сообщение
blasting coal technology process
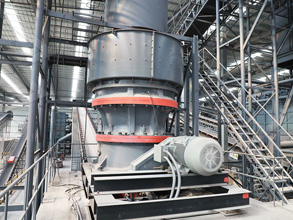
Drilling and blasting Wikipedia
Drilling and blasting is the controlled use of explosives and other methods such as gas pressure blasting pyrotechnics, to break rock for excavationIt is practiced most often in mining, quarrying and civil engineering such as dam, tunnel or road constructionThe result of rock blasting is often known as a rock cut Drilling and blastingOct 08, 2015· process of blasting in coal mines and use of shock tubeBlasting Technic and process
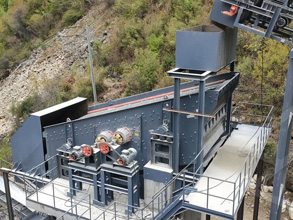
Economic Evaluation of Drilling and Blasting on the
Landau Colliery is one of Anglo Thermal Coal’s mines that want to investigate the economic impact of both the drilling and blasting process on the overburden removal process (Dragline), they want to know how the drilling process, blasting process and the earth removal process economically affect the mineThe US coal industry serves a vital role in the nation’s economy by producing fuel for more than half of its electricity Despite the industry’s importance, industry financial data for 2005—the strongest year for the coal industry in recent years—shows that it is aCoal Mining and Processing The National Academies Press
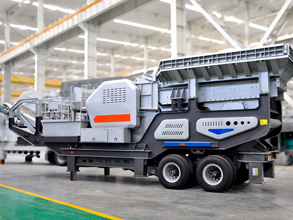
Citizen's Guide to Coal Mine Blasting in Indiana
typically used in surface coal mining to fracture the rock) After blasting, a dragline, shovels, trucks, or other heavy equipment remove the rocky overburden to expose the coal seam CITIZENS GUIDE TO COAL MINE BLASTING IN INDIANA Indiana Department of Natural Resources Division ofNational Institute of Technology Rourkela This is to certify that the thesis entitled “ Optimization of Blasting Parameters in Opencast Mines ” submitted by Sri Manmit Rout (Roll No: ) and SriOptimization of Blasting Parameters in opencast Mines
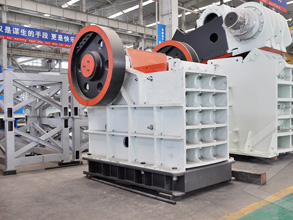
Understanding charging and blasting solutions for mines
Jan 07, 2020· Advantages of underground emulsion charging over ANFO charging are a 20% to 25% total cost savings Credit: Normet Before the invention of Tunnel Boring Machines (TBMs), drilling and blasting was the only costefficient way of creating longMay 13, 2020· Coal and gas outbursts are a major risk in deep gassy coal mines In order to minimize the outburst potential during the mining process, we proposeBlastingenhanced water injection for coal and gas out
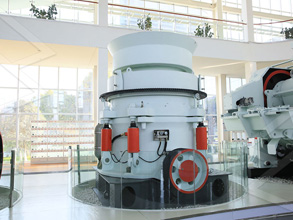
Surface Mine Blasting Office of Surface Mining
SURFACE MINE BLASTING Proceedings: Bureau of Mines Technology Transfer Seminar, Chicago, IL, April 15, 1987 Compiled by Staff, Bureau of Mines ABSTRACT The Bureau of Mines has sponsored a comprehensive research program to enhance the safe, effective, and efficient use of blasting technology by the mining industryIn book: Coal Production and Processing Technology, Chapter: Drilling and Blasting in Coal Mining, Publisher: CRC press, Editors: MR Riazi, Rajender Gupta, pp103123 Cite this publication Celal(PDF) Drilling and Blasting in Coal Mining
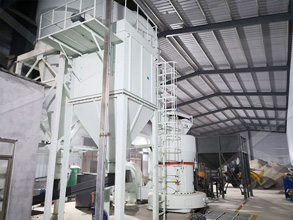
Blaster's Training Modules Module 4 Blasthole Drilling
A coal mine may encounter problems if it attempts to use the same diameter drill to blast overburden that is significantly deeper than the parting layer Fragmentation in the parting layer will be compromised, and flyrock may occur if blast holes are overloadedJun 14, 2018· A blasting agent is an explosive that: Comprises ingredients that by themselves are nonexplosive; c an only be detonated by a high explosive charge placed within it and not by a detonator All blasting agents contain the following essential components : Oxidiser – A chemical that provides oxygen for the reactionexplosives – Mining and Blasting
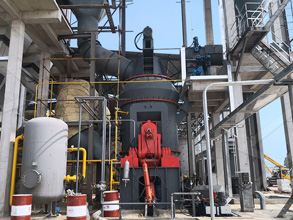
Blasting | Britannica
Blasting, process of reducing a solid body, such as rock, to fragments by using an explosive Conventional blasting operations include (1) drilling holes, (2) placing a charge and detonator in each hole, (3) detonating the charge, and (4) clearing awayThe blasting technology is the process of fracturing the material by the use of a calcula ted amount of explosive so that a predetermined volum e of material is broken down into pieces(PDF) ROCK BLASTING FOR MINING ResearchGate
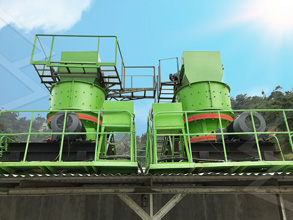
Black Magic® Coal Slag | Abrasives Inc
Description Black Magic ® coal slag is a recycled byproduct of lignite coalfired power plants Our slag is created from a hotter source which creates a harder material and conforms to environmental standards The extensive screening process we use to size our slag results in more consistently sized particles that are less likely to clog equipmentPellets technology ( ) Burden distribution control technology ( ) Blasting and injection technology ( ) Oil injection High temperature blasting Startup coal injection Waste plastics injection in Kakogawa No3 Annual Averaged 201 kg/thm Monthly averaged 254 kg/thm in Kakogawa No1 Steam injectionThe Principle of Blast Furnace Operational Technology and
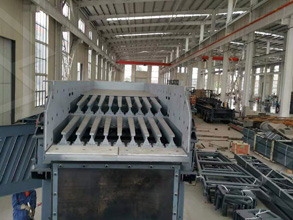
REDUCING COAL DAMAGE AND LOSS WITH A NEW
REDUCING COAL DAMAGE AND LOSS WITH A NEW BLASTING TECHNOLOGY Tapan Goswami 1, Geoff Brent 2, and Lloyd Hain 3 1Tapan Goswami, Principal Mining Consultant, Orica Mining Services, PO Box 196, Kurri Kurri, NSW 2327, Australia 2Geoff Brent, Research Associate, Orica Mining Services, PO Box 196, Kurri Kurri, NSW 2327, Australia 3Lloyd Hain, Drill & BlastJan 17, 2019· Coal is the largest source of energy for the generation of electricity worldwide and is also used in the production of metallurgical coke as blast furnace fuelSteel Manufacturing Process: Coal & Coke
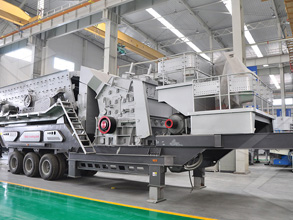
Blasting Safety – Revisiting Site Security
The bounds of the blast area were not adequately determined for this blast In a coal mine blast, flyrock traveled 900 feet and landed beyond the permit boundary causing a fatal injury [MSHA, 1990a] During a construction blasting operation near Marlboro, NY, flyrock was showered on passing motorists on Route 9 W about 180 feet from the blast pitCoal mining, extraction of coal deposits from the surface of Earth and from underground Coal is the most abundant fossil fuel on Earth Its predominant use has always been for producing heat energy It was the basic energy source that fueled the Industrial Revolution of the 18th and 19thCoal mining | Britannica
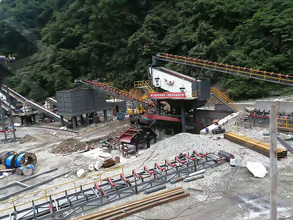
Productive Partnership – Advanced Blasting Technology at
blast method produced suboptimum results for both blasting and excavation, due to the varying geological strata’s Figure 1 – Wollombi Pit Coal Seam Layout & Photo of Seam Dip The initial process was to drill and blast down to the top of the coal seam or design RL, allowingPostblast nitrogen oxide fumes (NOx) from surface blasting activities have become an important operational issue in Australian Coal mines Postblast fumes are a direct product of the detonation process which can be easily identified as the resultant yellow to orange postblastUnderstanding main causes of nitrogen oxide fumes in
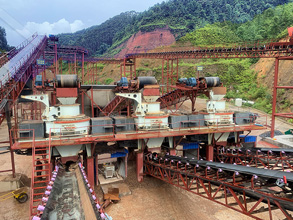
List of Technical Papers – Mining and Blasting
Blast design for Drifting and Tunneling with Wedge and Burn Cut; Over Burden Side Casting Advances in Drilling and Blasting Controlled Blasting Explosives, Ground Vibration and Air Blast Explosives and Blasting Blasting of Hot Holes in Opencast Coal Mines Blast Design in Opencast Mines and Concept of Optimum BlastingCoal mining, extraction of coal deposits from the surface of Earth and from underground Coal is the most abundant fossil fuel on Earth Its predominant use has always been for producing heat energy It was the basic energy source that fueled the Industrial Revolution of the 18th and 19thCoal mining | Britannica
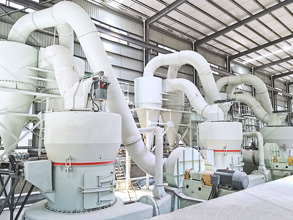
Productive Partnership – Advanced Blasting Technology at
blast method produced suboptimum results for both blasting and excavation, due to the varying geological strata’s Figure 1 – Wollombi Pit Coal Seam Layout & Photo of Seam Dip The initial process was to drill and blast down to the top of the coal seam or design RL, allowingPostblast nitrogen oxide fumes (NOx) from surface blasting activities have become an important operational issue in Australian Coal mines Postblast fumes are a direct product of the detonation process which can be easily identified as the resultant yellow to orange postblast cloudsUnderstanding main causes of nitrogen oxide fumes in
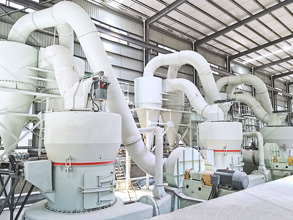
List of Technical Papers – Mining and Blasting
Blast design for Drifting and Tunneling with Wedge and Burn Cut; Over Burden Side Casting Advances in Drilling and Blasting Controlled Blasting Explosives, Ground Vibration and Air Blast Explosives and Blasting Blasting of Hot Holes in Opencast Coal Mines Blast Design in Opencast Mines and Concept of Optimum BlastingMar 16, 2015· SOLID BLASTING OF COAL(BOS) Both in Longwall and development faces coal can beblasted without giving an undercut by a coal cutting machine The technique of blasting of the solid is simpler, more economical and less hazardous than conventional method of breaking coal with machine cut and blastingExplosives and blasting in underground coal mining
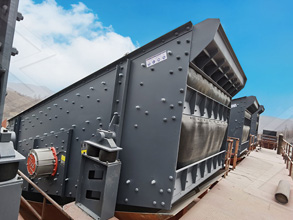
A Century of Bureau of Mines/NIOSH Explosives Research
years explosives and blasting safety research expanded from Pittsburgh, PA to include U labs in Minneapolis, MN, Denver, CO, Spokane, WA and College Park, MD Research grew from studies of newer explosives and blasting technology for underground coal mines to include applications for all types of mining During wartime thetechnology The opencast blasting approach involves breaking the coal‐rock mass for subsequent stripping Alternatively, the presplitting and blasting in deep boreholes aims at the formation of fractures inside the coal seam, the process is completed by the noncoupling charging and blasting in the coalPermeability improvements of an outburst‐prone coal seam
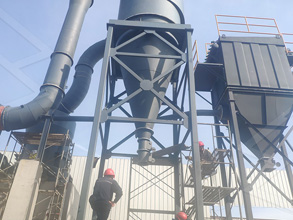
MIT develops technology that doubles efficiency and halves
Apr 04, 2016· The abundance of cheap and relatively clean burning natural gas as the result of the fracking boom has also made coal somewhat uncompetitive If the MIT technology can be made to work in the real world the decline of the coal industry could be reversed, placing the oldest fossil fuel back in the mix of energy sourcesCoal Advances in Boiler Cleaning Technology he said the process could destroy the wall or insulation of the boiler who went from blasting passes for roadways to using dynamite to cleanAdvances in Boiler Cleaning Technology | Power Engineering
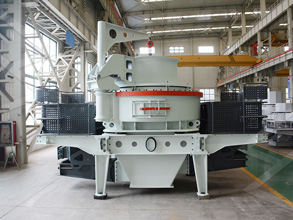
What is clean coal technology? | HowStuffWorks
Coal is a fossil fuel composed primarily of carbons and hydrocarbons Its ingredients help make plastics, tar and fertilizersA coal derivative, a solidified carbon called coke, melts iron ore and reduces it to create steelBut most coal 92 percent of the US supply goes into power production [source: Energy Information Administration]Blasting is the process where small angular or spherical particles are propelled at a part by compressed air, or mechanical high speed rotating wheels or water pumps The blast media type, shape, size, density, and hardness, along with media accelerationBLASTING TECHNICAL INFORMATION MC Finishing
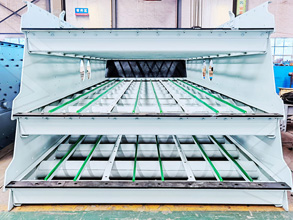
Blast Hole Drilling: The Basic Process | RPM Drilling
Basic Blast hole Drilling Process: Step 1 – Surveying the location Before the blast hole drilling can begin, the proposed site needs to be inspected, and certain decisions need to be made with regards to the hole size/diameter, the type of drill or drills that will be required, etcAdditionally, gamma logging delayed the blasting process for 24 hours as a result of manual data capture and analysis required to identify the coal seam Consequently, the mine’s drillchargeblast sequence required a minimum of three full days to complete; the mine recognized that by speeding up this process they could significantly increaseIndonesia Coal Mine Significantly Increases Blast
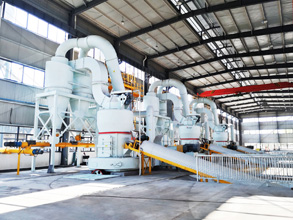
COREX EFFICIENT AND ENVIRONMENTALLY FRIENDLY
technology compared to the blast furnace route is the direct use of noncoking coal as the fuel/reducing agent and lump ore as the iron oxide feed While the use of fine coal via pulverized coal injection is available for both technologies, coal briquetting is applicable to the Corex only By coal briquetting it is possible to mix lowquality,