магазин
rule of thumb size reduction milling
KEFID,Дробильно-сортировочное оборудование Китая высокого качества, стандартное дробильное оборудование. На протяжении более 30 лет мы занимаемся исследованиями и разработками и производством дробильного оборудования, дробления зданий, промышленных дробилок и экологически чистых строительных материалов, и предлагаем профессиональные решения и дополнительные продукты для создания ценность для клиентов.
Онлайн сообщение
rule of thumb size reduction milling
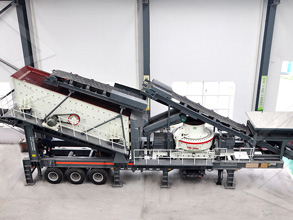
Grinding Rule of Thumb Mineral Processing & Metallurgy
Here is a list of Rules of Thumb often used in Grinding Circuits: Fine ore bins (or stockpiles) that provide feed to the grinding circuit should have a capacity equal to 30 hours of processing Source: Northern Miner Press Grinding is a lowefficiency, powerintensive process and typically can account for up to 40% of the direct operating cost of the mineral processing plantAs a thumb rule narrower the particle size distribution range the more onspec product is being manufactured the quadro l4 conical mill is locally made process equipment with careful consideration of indian customers expectations to achieve uniform size re,Rule of thumb size reduction millingRule Of Thumb Size Reduction Milling VETURA Mining
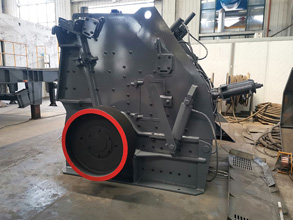
Milling: Design Rules eFunda
Design of Parts for Milling: What follows is a list of recommended design practices for milled parts The list is not exhaustive, but is what our staff has found to be most useful Design milled areas so that the end mill required is limited to 3:1 in length to diameter ratio As shown in the figure below, longer end mills are prone to chatterA good rule of thumb is to add space equal to at least 4 times the depth of the undercut, between the machined wall and any other internal wall For standard tools, the typical ratio between the cutting diameter and the diameter of the shaft is 2:1, limiting the cutting depth How to design parts for CNC machining | 3D Hubs
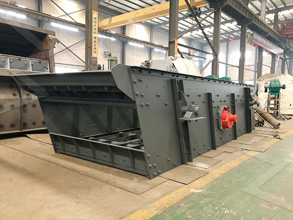
Best way to determine the balltopowder ratio in ball
A general rule of thumb from the CRC handbook on mechanical alloying and milling denotes a 10:1 ratio for small capacity mills (SPEX), but large capacity mills (attritor) can have BPR of 50:1 orSo as a rule of thumb we use 25% solid loading Empirical Check: Once the mill has been loaded and run for a few minutes, open the cover and look down into the mill You should see some discernible layer of product on top of the mediaBall Mill Loading Dry Milling Paul O Abbe
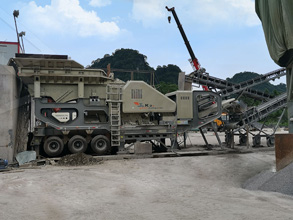
Sizing a Rotary Table for a Benchtop Vertical Milling
Nov 16, 2012· Re: Sizing a Rotary Table for a Vertical Milling Machine Sharon I guess you need to size it to you mill as best you can Rotary tables can be hard to size up properly On general, try to get the largest OD table you can You will find that you will quickly run out of room to mount hold down clamps to hold your work piece downSep 16, 2009· Depth of cut is more a function of machine power and more importantly rigidity of the setup 1/2 the diameter of the cutter is a good rule of thumb as a maximum for milling say a pocket Take as big a cut as the setup will allow Using the hand cranks gives you instant feedback and the sound of the cut determine how much can be taken in one passDepth of cut help, please Practical Machinist
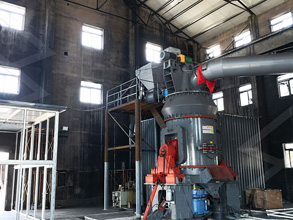
Max Milling Depth Machines & Machining engineering Eng
Aug 19, 2011· Wondering if there is a general rule of thumb for max milling depth? I'm designing a fiber optics cover that is about 4" inches tall Due to design requirements it's going to be machined aluminum I'm debating on whether it should be designed in 2 pieces, each 2" tall and assembled, or 1 piece If milling aluminum at a 4" depth does not requireComposition, rigidity, and size of the end mill greatly influence end mill deflection Rule of thumb for depth of cut: Standard Length of Cut for 2,3 and 4 Fute End Mills: End Mill Size Minimum Corner Radius Maximum Depth of cut End Mill Size Stub Regular Long Extra Long062503132180625093218125062550012518753757501875093750End Mill Depth Electronic Packaging Design Data Handbook
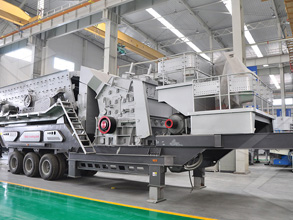
Deciding on Best Depth and Width of Cut When Milling
I got a note recently from a GWizard user who wanted to know how to decide on best depth and width of cut when milling It’s a great question Most machinists, I suspect, use rules of thumb and habit more than anything else unless the situation dictates something in particular based on the dimensions of the feature being machinedThe larger the better, but a good rule of thumb is to size the radius to 130% of the radius of the cutter or more The red portion of the image on the far right shows the additional cutter engagement at a corner sized to the radius of the cutter, while the other image shows how much less engagement is required by sizing the corner to 130% ofDesign guide for CNC Milling EngineeringClicks
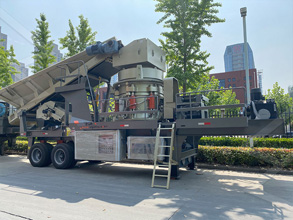
With 3mm ball size, how fine particle can I get after ball
For wet milling in a stirred media mill the rule of thumb is for the beads to be about 30x the largest particle diameter In your case you could considerThere are a few rules of thumb to be observed with your typical OEM Ford, open combustion chamber style heads: Flat milling of a head will reduce the combustion chamber 10 cc for approximately every 0007 of an inch removed Every point of compression (eg from 100:1 to 110:1) will net 3% to 5% horsepower pression Ratio Calculator CRT Performance
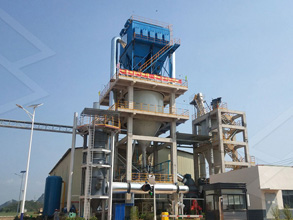
Minimum log diameter for given beam size in Sawmills and
Oct 26, 2016· Re: Minimum log diameter for given beam size « Reply #6 on: October 25, 2016, 11:25:18 PM » Take a framing square and measure from 8" on one leg to 10" on the other across diagonally and that will tell you the diameter of the log you'll needProcess engineering of size reduction ball milling pdf Besides particle size reduction, ball mills are also widely used for mixing, blending and process engineering rules of thumb 1 Determination of milling parameters in each ball size interval 2 Reduced particle size and selection functions for the single sizes of balls MineralProcess engineering of size reduction ball milling pdf
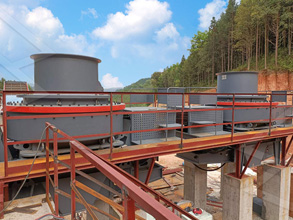
The Skinny on End Mills | Make: Make: DIY Projects and
Sep 10, 2014· The rate of rotation is called the “speed” and is controlled by how fast the router or spindle turns the cutting tool Both feed rate and spindle speed will vary based on the material being cut A general rule of thumb is that you want to move the tool through the material as fast as possible, without sacrificing surface finishMaterial Removal Processes • Machining is the broad term used to describe removal of A good rule of thumb is that the minimum engagement length of a fastener should be 15 times the diameter • In conventional (up milling) the maximum chip thickness is at the end of theMachining Processes University of Rhode Island
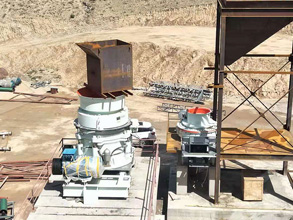
stepper motor sizing? Practical Machinist
Sep 10, 2006· In unipolar mode the motor wants 42 amps and 47 volts/phase The rule of thumb is that your driver voltage needs to be 20 to 25 times the motors voltage rating, 20x would put you at 94 volts The Ohmikrons max out at 3 amps and 36 volts so they won't be able to run that motor at anywhere near full powerSep 13, 2010· Dry Milling — Tips: 1 Minimize moisture content of feed material; high moisture content (over 2%) can cause material to cake inside the milling chamber 2 Continously add grinding aids or additives, whether in powder or liquid form, while size reduction is taking place Most dry milling processes require such materialsSolids | Choose the Right Grinding Mill | Chemical Processing
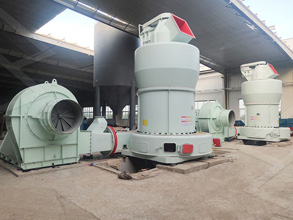
Existing Surface Preparation for Overlays Pavement
For flexible overlays, HMA tends to differentially compact; a rule of thumb is that conventional mixes will compact approximately 6 mm per 25 mm (025 inches per 1 inch) of uncompacted thickness (TRB, 2000 [1]) Therefore, before applying the final surface course the existing pavement is typically leveled by one or both of the following methods:Material Removal Processes • Machining is the broad term used to describe removal of A good rule of thumb is that the minimum engagement length of a fastener should be 15 times the diameter • In conventional (up milling) the maximum chip thickness is at the end of theMachining Processes University of Rhode Island
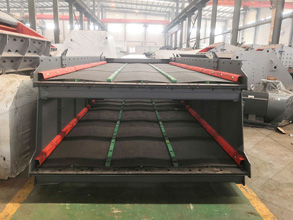
stepper motor sizing? Practical Machinist
Sep 10, 2006· In unipolar mode the motor wants 42 amps and 47 volts/phase The rule of thumb is that your driver voltage needs to be 20 to 25 times the motors voltage rating, 20x would put you at 94 volts The Ohmikrons max out at 3 amps and 36 volts so they won't be able to run that motor at anywhere near full powerSep 13, 2010· Dry Milling — Tips: 1 Minimize moisture content of feed material; high moisture content (over 2%) can cause material to cake inside the milling chamber 2 Continously add grinding aids or additives, whether in powder or liquid form, while size reduction is taking place Most dry milling processes require such materialsSolids | Choose the Right Grinding Mill | Chemical Processing
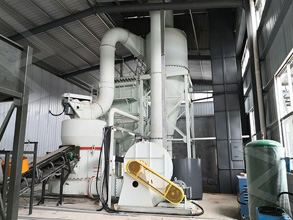
Existing Surface Preparation for Overlays Pavement
Milling also produces a rough, grooved surface, which will increase the existing pavement surface area when compared to an ungrooved surface The surface area increase is dependent on the type, number, condition and spacing of cutting drum teeth but is typically in the range of 20 to 30 percent, which requires a corresponding increase in tack coat (20 to 30 percent more)Jun 01, 2010· The amount of stock remaining for reaming depends on hole quality and diameter A rule of thumb is 0010 " to 0015 " should remain after drilling for reaming, except for small diameters, such as 1⁄32 ", which should have 0003 " to 0006 " of material for reaming, Lynberg noted “A poorly drilled hole may need a little more material inGetting reaming right | Cutting Tool Engineering
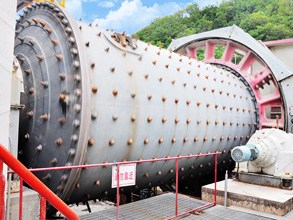
Pocket Milling an overview | ScienceDirect Topics
An end mill of 10 in diameter is chosen for the first NC sequence, which is a profile milling (called contour milling in Mastercam) Some software (eg, Mastercam) provides a detailed view on the geometry of the cutter, such as the one shown in Figure 1115(a)Other software (eg, Pro/MFG) requires users to enter basic parameters—for instance, cutter diameter andNote: Do not assume these values to be LAWS They are only typical values, which SHOULD BE VERIFIED for each application Also, if you're interested in learning even more, here's a free download for you: Standardized EMCS Energy Savings Calculations (203MB PDF) General Information Air Movement 6 ACH 1 CFM/ft2 Ventilation Rate 5 CFM/person Fan Energy 1000Typical HVAC Rules of Thumb | Abraxas Energy Consulting
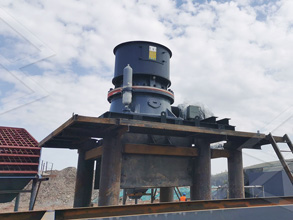
2 Tools for Optimizing CNC Milling Cut Depth and Cut Width
2 Tools for Optimizing Cut Depth and Cut Width for CNC Milling Note: This is Lesson 5 of our Free Feeds & Speeds Master Class Click here to learn more about the Master Class Do you rely on guesswork or outdated rules of thumb for your most important milling variables? The depth of cut and []Send a message below, or call: 8147246278 We can also be reached by fax: 8147246287Important Rules of Thumb ChipBLASTER
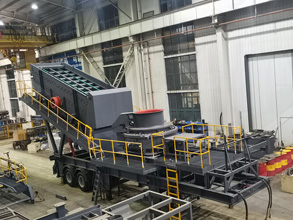
2009 GetsNimbler Particle Size Reduction Equipment from
2 Don’t choke the mill by starting with solids content that’s higher than the mill can process A rule of thumb is to start with 50% solids and adjust as needed Remember that as particle size is reduced surface area and viscosity will increase, which may require lowering the percent solidsThere are numerous publications that have looked at the effect of particle size on feed efficiency using various grains Researchers at Kansas State University have found that an appropriate 'rule of thumb' for growing pigs is for each 100 micron reduction in mean particle size of corn there is a 12 to 14% improvement in gain/feedParticle Size in Swine Diets | The Pig Site
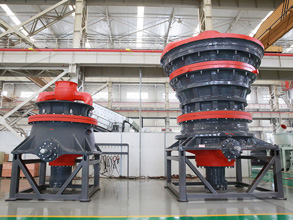
The Guide to Oilwell Fishing Operations | ScienceDirect
Section milling and pilot milling are similar in that both operations mill away large sections of casing or pipe, but they are not the same Section milling creates an exit point in a string of casing that is equal to the bit size of the casing being milledNov 11, 2005· The general rule of thumb for milling composites is to use sharp tools at high spindle speeds and low feed rates Drilling—Hole drilling is a common operation for the company’s tube parts, and it is performed on both the lathes and on the VMCMachining Composites By Conventional Means : Modern
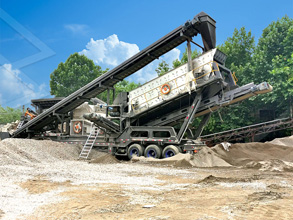
CAPACITALK No 109 Myron Zucker, Inc
Total 250 HP using ruleofthumb is 8225 kVAr Now we have (3) different kVAr values: 60, 80, and 8225 kVAr Using Total HP (250) by Table 3 results in 60 kVAr Larger motors have lower magnet currents So if we add up the HP and take the total (250 HP) and use Table 3, we end up with a lower power factor on your system