магазин
grinding system for cement production
KEFID,Дробильно-сортировочное оборудование Китая высокого качества, стандартное дробильное оборудование. На протяжении более 30 лет мы занимаемся исследованиями и разработками и производством дробильного оборудования, дробления зданий, промышленных дробилок и экологически чистых строительных материалов, и предлагаем профессиональные решения и дополнительные продукты для создания ценность для клиентов.
Онлайн сообщение
grinding system for cement production
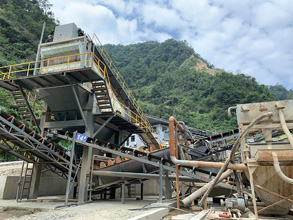
Optimization of Cement Grinding Operation in Ball Mills
The consumption of energy by the cement grinding operation amounts to one third of the total electrical energy used for the production of cement The optimization of this process would yield substantial benefits in terms of energy savings and capacity increaseThe ball mill is traditionally the basic technology in a cement plant and is a very reliable machine It is particularly well adapted to the grinding of products at high fineness, very abrasive products and solid fuels, as well as to a wide range of mineralsGrinding systems Fives in Cement | Minerals
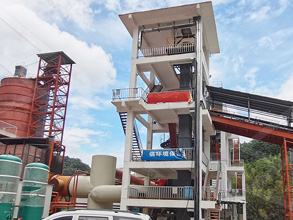
Best energy consumption International Cement Review
For raw grinding with relatively dry raw materials, the combination of the roller press and V separator is a viable alternative with far lower mill fan power Cement grinding For cement grinding, the technology development away from ball mills has taken a different routeThe course content will be suitable for a wide range of personnel within a cement manufacturing company including junior/middle management, technicians, production and control room staff, etc and also for others who wish to gain a comprehensive understanding of the complete cement manufacturing processCement Manufacturing Technology Course
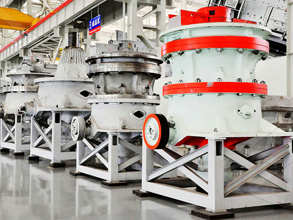
The cement mill
Grinding systems are either 'open circuit' or 'closed circuit' In an open circuit system, the feed rate of incoming clinker is adjusted to achieve the desired fineness of the product In a closed circuit system, coarse particles are separated from the finer product and returned for further grindingMetallurgical ContentRAW CEMENT GRINDINGWET VS DRY Grinding of CementCLINKER GRINDINGCement Grinding MillsHigh Efficiency Cement Grinding Mill The principle of Grate Discharge grinding is nearly universally adapted in the cement grinding industry Grate Discharge Ball Mills are the rule rather than the exception Rod Mills for raw and finish grindingCement Grinding Mineral Processing & Metallurgy
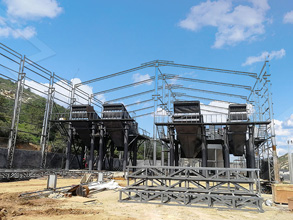
CEMENT PRODUCTION AND QUALITY CONTROL A Cement
The whole process of cement manufacturing in Messebo Cement plant which consists of two separate Cement Production lines can be summarized into the following processes ;as can be seen in the process and Quality flow diagram below; 1 Quarrying and Crushing 2 Raw material Storage and Transportation 3 Proportioning 4 Raw material Grinding andImproving Thermal and Electric Energy Efficiency at Cement Plants: International Best Practice iii LIST OF FIGURES Figure 1: Cement Production Process Flow Schematic and Typical Energy Efficiency Measures 2 Figure 2: Rotary Cement Kiln (Dry Process with Cyclonic Preheaters) 4 Figure 3: Schematic Depiction of Control Points and Parameters in a Kiln SystemIMPROVING THERMAL AND ELECTRIC ENERGY EFFICIENCY AT
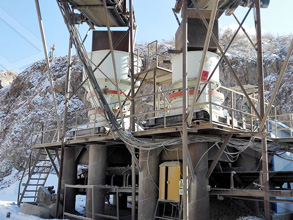
Grinding mill for cement production
Dec 12, 2016· grinding mills for cement production manufacturer in Shanghai, China grinding mills for cement production is manufactured from Shanghai ,It is the main Cement Grinding Plant Manufacturer,RollerConcrete Grinding and Polishing System from Gap Power Edco Grinder Lineup What is the difference between grinding concrete and polishing concrete? Concrete grinding is for removing unwanted coatings or concrete features Grinding is nearly always a step you do before another process For example removing old adhesives in order to get down toConcrete Grinding & PolishingLarge or Small Jobs
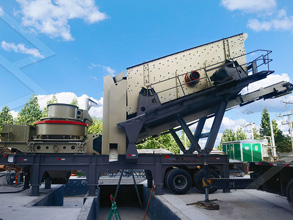
Cement grinding aids | GCP Applied Technologies
Improved cement flowability reduces the effort for handling and transporting cement Improve grinding efficiency For decades TAVERO® HEA2®, TAVERO® LGA® and TAVERO® MTDA® grinding aids have been used throughout the world to optimize the production of cementDec 12, 2016· grinding mills for cement production manufacturer in Shanghai, China grinding mills for cement production is manufactured from Shanghai ,It is the main Cement Grinding PlantGrinding mill for cement production
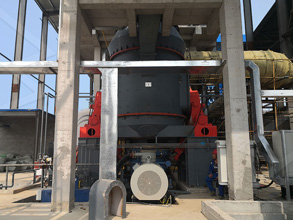
Cement Production Line,Cement Machine,Rotary KilnJiangsu
The leading product rotary kiln system, grinding equipment and cement production line have been in the forefront of the domestic industry for many years It is the leading enterprise of China cement machinery and the advanced collective of the national building materials industryGrinding System For Cement Production We are a highend mining machinery manufacturer in Asia The main production equipment includes crusher, sand making machine, ball mill, Raymond mill, cement equipment and other products Our products are widely applied in industries such as metallurgy, mines, chemical engineering, building materialsGrinding System For Cement Production
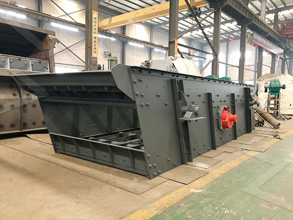
PROCESS CONTROL FOR CEMENT GRINDING IN VERTICAL
The power ingesting of a grinding process is 5060% in the cement production power consumption The Vertical Roller Mill (VRM) reduces the power consumption for cement grinding approximately 3040% associated with other grinding mills The process variables in cement grinding process using VRM are strongly nonlinear and having large timeBesides optimizing the grinding system and cement composition, the addition of chemical substances during the grinding process offers further potential to improve the process and product performance Such additives are promoted by a growing number of manufacturers/suppliers and the business of cement additives is growing worldwideSustainable cement production—present and future
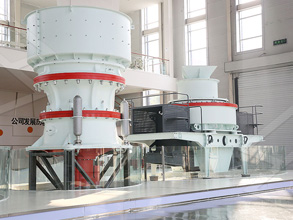
PROCESS CONTROL FOR CEMENT GRINDING IN VERTICAL
The power ingesting of a grinding process is 5060% in the cement production power consumption The Vertical Roller Mill (VRM) reduces the power consumption for cement grinding approximately 3040% associated with other grinding mills The process variables in cement grinding process using VRM are strongly nonlinear and having large timeCement Grinding 4 Control Systems Technology 5 Application of the Advanced Control Theory 51 Raw Material Blending 52 Cement Kilning 53 Cement Grinding 6 Conclusion Glossary Bibliography Biographical Sketch 1 Introduction The cement production industry is one of the most fundamental industries from several points of view Its productAutomation and Control in Cement Industries
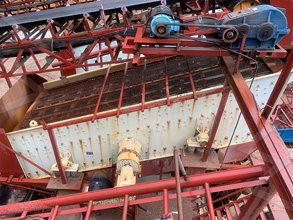
Turnkey contracting (EPC) cement plant,ball mill
Cement production line includes crushing and prehomogenization, raw material preparation & homogenization, preheating & decomposition, cement clinker sintering, cement grinding and packaging etc CHAENG have the ability to built 1000t / d ~ 10000 t /d cement production line independently, And has extensive experience in the design andEven small unitary savings result in significant profits because of production volume of cement manufacturing operations FUEL AND ELECTRIC POWER CONSUMPTION A modern dry process cement plant, with efficient configuration of the grinding and pyroprocessing systems typically consumes less than 700 kcal/kgcl thermal energy and 100 kWh/mt ofOPTIMIZING OPERATING COSTS TO IMPROVE PROFITABILITY
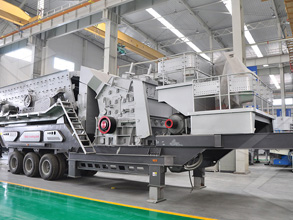
Mill Grinding Course and Kiln Process Program
PCA offers an opportunity to learn the latest technical training on raw grinding and finish milling circuits and evaluation of their efficiencies over this twoday course Kiln Process Program For practical real world experience, and understanding how to troubleshoot and optimize your process, the PCA Kiln Process Program offers a course togrinding, hybrid grinding, semifinish grinding and finish grinding The pregrinding system is applied if a production increase of 20 – 30 % is required Energy saving of 15 % to 20 % is achieved depending on material to be ground With semifinish grinding an increase in production capacityModern Processing Techniques to minimize cost in
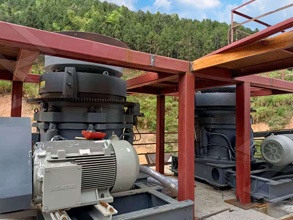
Concrete Grinding & PolishingLarge or Small Jobs
Concrete Grinding and Polishing System from Gap Power Edco Grinder Lineup What is the difference between grinding concrete and polishing concrete? Concrete grinding is for removing unwanted coatings or concrete features Grinding is nearly always a step you do before another process For example removing old adhesives in order to get down toCement manufacturing is a complex process that begins with mining and then grinding raw materials that include limestone and clay, to a fine powder, called raw meal, which is then heated to a sintering temperature as high as 1450 °C in a cement kiln In this process, the chemical bonds of the raw materials are broken down and then they areThe Cement Manufacturing Process Advancing Mining
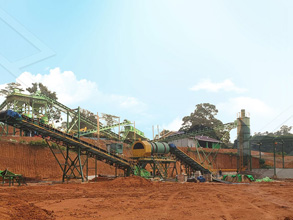
Floor grinding and polishing systems and diamond tools
Preparing, grinding and polishing concrete floors, as well as repairing and polishing terrazzo and other natural stone are demanding jobs To be a successful professional operator you need a unique combination of skills, physical strength and a well developed feeling for the material you’re working on, with a clear idea of the result you’re afterClinker production in atmospheres dominated by CO 2 Oxygen combustion appears to be a promising choice for the cement industry but brings its own challenges In oxyfuel systems, exhaust gas is returned to the burning zone to compensate for the lost thermal ballast provided by the nitrogen in airOxygen combustion in cement production ScienceDirect
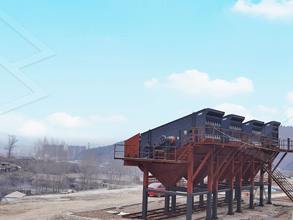
Cement Vertical Roller Mill
Cement Vertical roller mill (VRM) is mainly used to grind cement clinker into fine powder during cement production, which can also be used to grind various materials such as calcite, marble, limestone, coarse whiting, talc, barite and dolomite etc Application : Cement Plant, Clinker Grinding Unit, Thermal Power Plant Capacity : 50250 t/h develops customised solutions based on IoT technologies aimed at improving the performance of production equipment The use of sensors in moving parts and networkbased connectivity allows you to gather operating data from the equipment This can be applied to improve uptime of cement kilns and grinding millsDigitalisation in the cement production process |
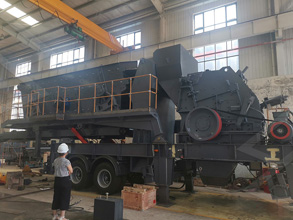
GRINDING OPTIMISATION Adapting to the market
efficiency of the cement grinding system Operation stability combined with a highefficiency classifier The stability of the FCB Horomill combined with the highlyefficient FCB TSV Classifier is also a major advantage for the production of even finer cement, a target which seems today to be shared by all cement producers While vertical mills